A Carisbrooke Shipping bulker is about to leave a refit yard in Hull, northeast England, with a very visible addition.
It is a wing sail propulsion system fastened on the forecastle of the 10,260-dwt Vectis Progress (built 2012), somewhat off the portside of its centreline.
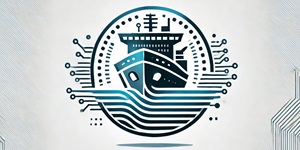
It is not the first ship to have a wind propulsion system installed, and probably not the last, but for GT Wings, the British company behind the technology, it is a first.
The final touches are being made to the vessel and the system to ensure the old and new will work together.
The Vectis Progress sits at MMS Ship Repair’s yard in Hull’s Alexandra Dock, surrounded by huge wind turbine blades ready to be exported around the world, a cargo that the vessel sometimes carries.
Carisbrooke, GT Wings and the University of Bristol are part of a project with grants awarded from the UK’s clean maritime decarbonisation competition, a funding scheme that has been supporting the country’s maritime clean-tech and digital sectors for the past four years.
Its sixth round was announced last month with £30m ($38m) available for new projects.
The challenge for the WindWing project partners has been the limited time frame the government gave them to complete the project — in other words, to build, plan and install a system on a ship in a year.
One does not just bolt a wind propulsion system onto a ship and expect it to sail into the wind. The process requires careful preparation, including assessing its impact on line-of-sight visibility, cargo operations, navigation and overall performance.
Then there is the work on board to lift the 20-metre-high rig onto the forecastle — the ship has its own two cranes on its starboard side.
GT Wings chief executive George Thompson said: “It was an emotional moment when I saw it on the ship, upright.
“I didn’t realise just how tall it would look on the forecastle.”
The task of welding, cutting, bolting together parts and then linking the cables fell on the vessel’s crew, company superintendents and a few of the shipyard personnel.
The installation was carried out day and night, along with other work the company decided to do while it was alongside for a month.
A surveyor from classification society Bureau Veritas was on hand to ensure everything was in order.
One challenge for Thompson and GT Wings has been that the team has not had time to perform land-based trials that other wind propulsion outfits have been able to do ahead of prototypes being installed.
That was down to the tight time frame the government gave the team as a stipulation for funding.
The wing was made and ready at MMS in Hull until the Vectis Progress came into the dock at the end of January.
“The wing is 34 tonnes in weight,” Thompson said. “The plinth it sits on is about seven-and-a-half tonnes, and I am told there is about five tonnes of extra steel and a tonne-and-a-half of cabling.”
A balancing act
A visit into the cramped forward area under the forecastle revealed areas where the steel has been thickened and masses of cables have been fed back through pipe ducts.
The team estimated that the installation has added well over 50 tonnes to the lightweight of the ship, enough for it to need to recalibrate its stability calculations.
Under class rules, if the centre of gravity, longitudinal centre of buoyancy or lightweight of the ship changes by more than 1% or 2%, the stability needs to be recalculated, a process known as the re-inclining tests.
Huge concrete blocks were placed on the decks and large pendulums were hung in the cargo hold waiting for the tests to start once the rig components were all in place.
The Canadian authorities have also had a lot of say in what can be done with the installation.
The Vectis Progress is on a long-term charter with Canadian shipowner Fednav, taking cargoes in and out of the Great Lakes through the St Lawrence Seaway, which has its own width, draught and air draught limitations.
As a result, the forward mast has been relocated, cameras have been fitted for added visibility and an additional radar sits on the bow.
These adjustments — installation and cabling, and then safety checks — take time, which means the vessel is not available for Fednav to offer to cargo owners.
But, for Fednav, the rewards will be in lower fuel bills.
The nascent technology may become the next big thing for shipping’s fuel efficiency drive and Carisbrooke could potentially order more if this initial unit proves its worth.
The sea trials and the first voyage of the Vectis Progress will be nervous times for Thompson, who plans to be on board the initial voyage from the UK to Spain to load, and then to Canada.
“There are already improvements we plan on making from what we have already learned,” he said, noting that the company has two investors who understand the time frames needed and the risks of installing new technology into harsh environments.
“Obviously this first wing has taken longer to install, but future wings should be much quicker, and we expect choreography around the ship in port to be much smoother.”
The International Windship Association estimates there are about 70 vessels with various wind propulsion systems installed and about 80 more waiting to have them fitted.
One type is solid wing sails, which act a bit like a vertical aeroplane wing and do not require any power. BAR Technologies and Smart Green Shipping have developed examples of this type of system.
Then there are Flettner rotors, from companies such as Norsepower and Anemoi Marine, which spin to help create thrust.
Suction wings draw air into the large structures, and in doing so keep the air tighter to the surface of the wing, preventing turbulence and generating more lift. Econowind and Bound4Blue have developed this technology.
GT Wings claims to have a new system. It has a suction element due to a series of fans pulling in air up the turret, but they also pump the air out onto the back element of the wing to improve efficiency.
The fans can all act independently, as wind strength up a sail can vary, a condition known as wind shear. Varying the speed of the fans helps ensure the wing maximises the wind shear.(Copyright)