The first thing someone does when they get their hands on one of Pelagus 3D’s printed parts?
They try to break them.
“As soon as they notice 3D printing, the first thing they want to do is test breaking strength, like how far can I go before it breaks?” said Wilhelmsen vice president for emerging opportunities Nakul Malhotra.
But the parts, made with the consent of equipment manufacturers and close to the point of need, prove sturdy: “The first thing is to get used to the fact that additive manufacturing is just another manufacturing process. Don’t stress about it,” he said.
In the company’s telling, that was the first hurdle to clear in making 3D printing in shipping — considered by some a promising development that could decrease vessel downtime — a reality.
With the breakage issue settled, Pelagus 3D is finding push factors for owners, managers and part manufacturers. Namely, sustainability.
Making a pump
Wilhelmsen and Thyssenkrupp-backed Pelagus 3D is not shipping’s first foray into 3D printing, or even Wilhelmsen’s.
The Oslo-listed holding company kicked the tyres on 3D printing roughly a decade ago with a separate start-up. Maersk Tankers also explored possibilities with onboard 3D printers, a programme it later shuttered.
Kongsberg Maritime has used 3D printing to make prototypes and the American Bureau of Shipping joined with Polar Tankers to trial 3D printed parts in 2021.
Pelagus 3D appears to have made more headway. The company has agreements with 21 equipment manufacturers and 25 end users, including ship managers such as Bernhard Schulte Shipmanagement and Hafnia.
One of those agreements saw the company 3D print a return oil standpipe for the Wallenius Wilhelmsen-owned 6,000-ceu car carrier Tysla (built 2012). The part was originally manufactured by Kawasaki Heavy Industries and installed in October 2023.
Pelagus 3D chief executive Kenlip Ong said the Japanese equipment manufacturer carries few replacement return oil standpipes, which are seldom needed and expensive to store.
So the company redesigned the part for 3D printing, fabricated it in Kobe, Japan, and delivered it to the ship in the port.
“This part itself has a huge lead time of 135 days, and weighs 75 kilos,” said Ong, regarding the conventional part.
“So there’s a lot of savings that goes into [3D printing the part] as well. Through 3D printing, we can produce an equivalent in 15 days that weighs 7.5 kilos.”
Additionally, he noted that it saves time and simplifies installation, as it can be done by one person instead of three, without the need for a crane, extra materials or storage.
Cutting emissions
It also saved Kawasaki and Wallenius Wilhelmsen the emissions from fabricating and shipping the traditionally made part.
Malhotra said the growing focus on cutting emissions and sustainable shipping has increased interest in Pelagus 3D’s services.
Manufacturing parts on-demand and close to the source of need helps owners and operators cut their Scope 3 emissions, or those related to business activities they have no control over, he said.
“There’s going to be an increasing need for transparency along the absolute ends of the chain,” Malhotra said, likening Pelagus 3D’s services to the parts equivalent of well-to-wake or tank-to-wake emissions.
“Like all things, you’re going to have some earlier movers. There’s later movers, but everybody’s moving.”
The concept is ultimately to establish a digital warehouse for those seldom-needed, hard-to-get or even obsolete parts, which Pelagus 3D estimates could be as much as 40% of equipment manufacturers’ catalogues.
The company has established an online back-end where equipment manufacturers can upload part files and criteria to allow clients to easily request the parts necessary.
Ong calls it a digital warehouse.
“That means that I save on not having these parts being manufactured and shipped around the world multiple times, to central warehouses, to regional warehouses and taking up space in an actual physical storage warehouse,” he said. “There is no taking up of capital in doing that.”
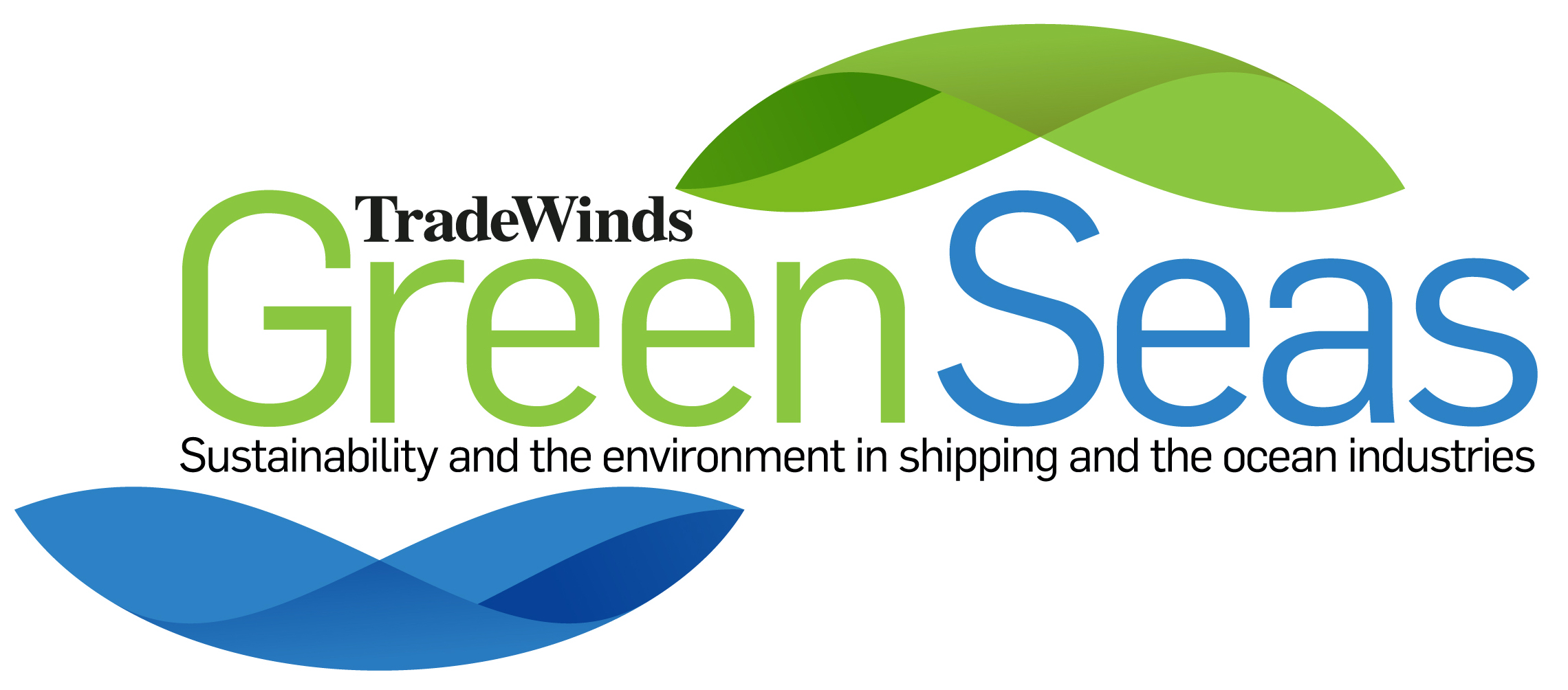